Our Quality Process
Since we work with systems that should last 25 years and always work perfectly, quality is the Alpha and Omega of our business.
We work according to a given quality process in each step, which is described and exemplified below.
1. Request. Customer needs. Offer. Order.
For us, it is crucial to understand our customers’ requirements and specifications in every project. We rarely say no. We often make specially adapted solutions for our customers, e.g. divisible units, if there are tight spaces, or if a new pump is to be adapted to an existing equipment.
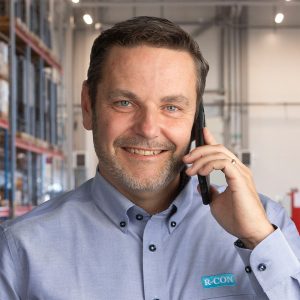
2. Construction. Planning.
Based on the agreed solution with the customer, we create construction and drawings, followed by assembly instructions in our production. In this phase, we also do production planning and purchases, which come from all over the world. In larger projects, regarding tanks and pump houses, project planning is done.
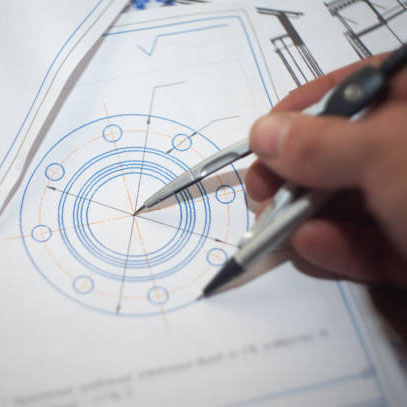
3. Production, incl. Factory Tests.
All orders in our production are made according to an assembly instruction, following the agreed specification. Our production is divided into several departments. Before a pump leaves our production, a full-scale factory test is carried out, where the pump is connected and tested according to a predetermined schedule. In this way, we can ensure the highest quality. As we usually say: We’d rather find a problem here, than at the customer’s facility.
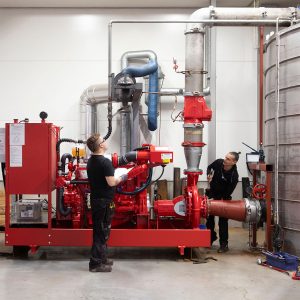
4. Physical Delivery.
Schenker takes care of our deliveries, with pick ups on Fridays, so that our goods are at the customer’s facility on Monday. Before delivery, we photograph all parts and make sure that everything is included. Our products are placed in protective special packaging in wooden boxes. Our delivery reliability in the last 12 months was 99.2%, which we are very proud of. We always check with the customer before delivery. We also make customised deliveries, such as time specific unloading, using crane truck and adaptation to heights.
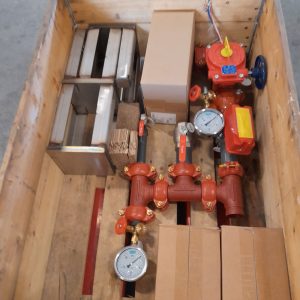
5. Installation and Installation Support.
Our customers usually do the installation of our pumps, and we do the electrical installation. To make things easier, clear installation manuals and markings on the pumps are included. Accessories for assembly are included. When working on the customer’s construction site, we always ware ID06 or SSG.
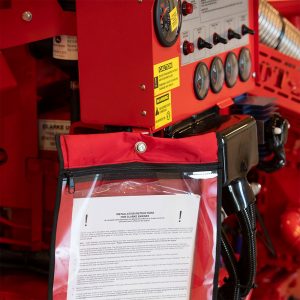
6. Warranties. After Market. Follow-up.
The occasional times when something goes wrong, we solve it quickly and easily. It should not affect you as a customer. With our long experience, we usually solve it by phone and e-mail, but if that is not enough, we will come to your facility and solve it on site. In the case of warranty matters, of course we provide the same warranty as our customers need to provide to their clients.
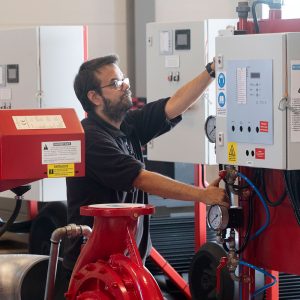
We Know the Extensive Regulations
There is an extensive set of regulations regarding fire protection, partly locally in Sweden, Denmark, Norway, partly for the whole of Europe. We have a long experience and a deep knowledge of these regulations and we follow ongoing changes.
We supply pumps and equipment according to the following regulations and standards:
- Sweden: SBF120:8, SSEN12845, SBF 501:2/SS-EN 16925:2018
- Norway: NSEN12845, NS-EN 16925:2018 and FG approved
- Denmark: DBI 251/4001 udgave 3 2021
- Europe. International: FM, LPS, VDS and NFPA 20
We Work Sustainably – Step by Step
We are about to take another step in our work for increased sustainability: We will install solar cells on our customers’ pump houses. In this way, they will become self-sufficient in energy. A great environmental effect! We have already installed solar cells at our test and training facility, which you can visit for a demo.
Another step in our sustainability work, is to promote the changing of regulations in the industry, allowing us to control the pumps remotely. It would save a great deal of travel for our service technicians and our customers.
For long, we have contributed with positive effects in several ways:
- Our products last a long time, normally 25 years
- Our modern property built in 2020 has a very low energy consumption
- We recycle in eight fractions in our facility: plastic, wood, electronics, environmentally hazardous waste, fluorescent tubes, batteries, corrugated cardboard, and office paper.
- We have our own repair workshop, to recycle products and extend lifespan.
- Our diesel sprinkler pumps are powered by Ecopar, an environmentally friendly fuel produced from garbage.
- All our service cars can be driven on HVO or Ecopar
In addition to this, all our solutions in general have a positive sustainability effect, as they protect assets from fire and damage.